Wick Assemblies: A Primer
We get tons of questions about wick assemblies every day at CandleScience. This article describes what a wick assembly is, how it's made, and what each component does.
Raw Wick
At the core of all assemblies is the raw wick. Raw wick refers to the woven fibers alone without wax coating or tabs. The raw wick does all the work of burning the candle and can be used on its own. Using wick assemblies just simplifies the candle making process.
Wax Coating
The first step in making wick assemblies is to coat (or prime) raw wick with wax in a coating machine. The machine feeds wick through a bath of melted coating wax filled with a number of pins that bend the raw wick, forcing out any air as the wax fully saturates the fibers. Several passes are required to achieve the desired wax thickness. After coating the wick is re-spooled, and referred to as coated (or primed) wick. It is sometimes sold this way in smaller spools for making pillars.
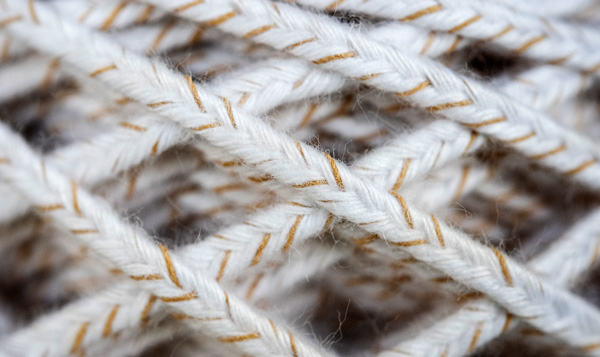
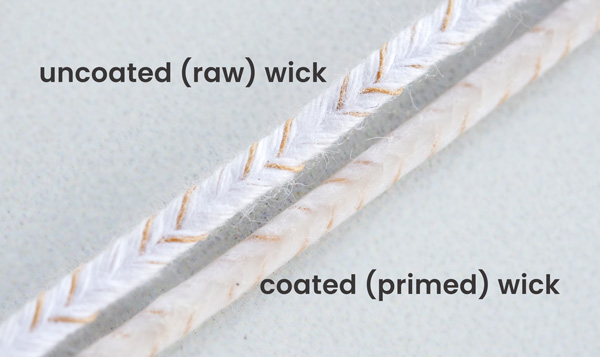
The main purpose of coating wick is to add rigidity to the assembly when it is inserted into a container. A proper wick coating wax is hard but pliable and has a reasonably high melt point. Many different types and blends of wax can be used to coat wick without affecting the performance of the wick.
CandleScience has recently switched all of our wicks to a natural coating. Natural candle makers can market their products as 100% natural wax all the way down to the wick, and paraffin candle makers don't notice the difference.
An interesting thing to note; once a wick is coated with wax, it is nearly impossible to determine the small difference between various wick sizes. Because the type or amount of wax added to the wick does not affect the burn the thickness is not precisely controlled. So while raw LX-10 has a smaller diameter than raw LX-18, they may appear similarly sized once coated.
Often people receive a new bag with a little more or less wax than their previous batch and suspect they received the wrong wick. Don't worry, it's just coating thickness, you can trust the wick is exactly as labeled.
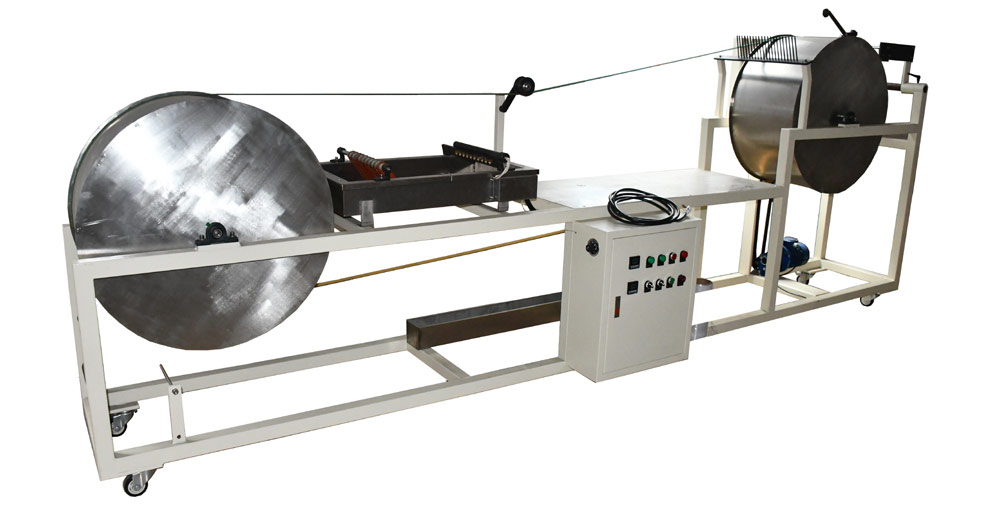
Cutting and Tabs
After coating the spools are moved to the wick tabbing machine, where the wick is cut to a selected length and the safety tab (or sustainer tab) is crimped onto the end. The tab serves a number of purposes. Its primary job is to give the wick a foot to stand on when placed in a container and to hold the coated wick straight during the life of the candle.
Its secondary job is to extinguish the wick before it reaches the absolute bottom on the container. The higher the neck, the farther from the bottom of the container the wick will burn out. This prevents unwanted heat transfer through the bottom of the container into the surface below. CandleScience just switched to a slightly larger tab with a longer 'safety' neck on all our wicks.
Related Links:
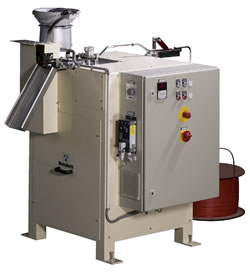